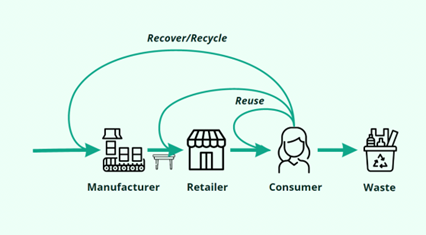
In an era where climate change is accelerating, environmental awareness and sustainability have become of paramount importance. One effective way to address these concerns is through remanufacturing, which is increasingly being adopted across various industries.
The reasons why remanufacturing constitutes such a pivotal practice in the modern industrial landscape, are diverse and intriguing. Foremost, it embodies a sustainable approach to production and consumption, opposing the pervasive culture of disposability by extending the lifecycle of products. By reconditioning used items, remanufacturing significantly reduces the demand for new raw materials, thereby mitigating resource depletion and environmental degradation. Moreover, it fosters the transition towards a circular economy, where products and materials circulate in closed-loop systems, minimizing waste and maximizing value retention. Economically, remanufacturing offers substantial cost savings compared to producing new goods, contributing to enhanced profitability for businesses while promoting supply chain resilience. Beyond its tangible benefits, remanufacturing also aligns with shifting consumer preferences towards environmentally conscious products and practices, which not only enhances market competitiveness but also increases public awareness about sustainability.
Overcoming Challenges in Remanufacturing
Certainly, it’s essential to acknowledge some of the challenges facing remanufacturing initiatives thus far. Despite its promising potential, remanufacturing has encountered hurdles that have hindered its widespread acceptance. One significant issue is the lack of standardized processes and technologies, leading to inconsistencies in product quality and reliability. Additionally, there are concerns about the perception of remanufactured products among consumers, who may associate them with lower quality or stigma. Furthermore, there are also logistical challenges, since processes for managing the return, refurbishment and disposal of products or materials most of the time are not optimized, leading to delays, increased costs or inefficiencies in materials handling. Lastly, remanufacturing practices have also faced limitations due to recycling regulations while obtaining or acquiring used or recycled parts or materials necessary for the process. Lastly, remanufacturing practices have also encountered constraints imposed by recycling regulations when seeking to obtain or acquire the used or recycled parts or materials necessary for the process, emphasizing the importance of creating supportive regulatory frameworks that encourage and facilitate the remanufacturing process.
The R3-Mydas advantage
The aforementioned hurdles underscore the need for innovative solutions and collaborative efforts, like the R3-Mydas project, to overcome barriers and unlock the full potential of remanufacturing in creating a more sustainable and resilient industrial landscape, focusing on industries such as Oil & Gas, electric vehicles (E-vehicles) and wind turbines;
- In the Oil & Gas sector, the lifecycle of the equipment will be extended to achieve the elimination of waste and carbon footprints.
- In the E-vehicles sector, batteries usage will be repurposed at the end of their lifespan, to reduce landfill waste and preserve valuable resources like lithium and cobalt.
- In the Wind turbine sector, remanufacturing wind turbine gearboxes involves utilizing high-quality materials, thereby reducing the environmental impact typically associated with manufacturing new gearboxes.
The project aims to standardize remanufacturing processes, evaluate their environmental and socio-economic impacts, and explore new value chains with an emphasis on safety, training, logistics, ethics, and liability. It will employ cognitive robotics and quality control predictive models to optimize processes and develop a digital marketplace for remanufactured products and services.
ITML’s role
Within R3-Mydas, ITML utilizes its proprietary technology and offers Analytics-as-a-Service for the demo case on remanufacturing E-vehicle batteries. Key activities include implementing an Internet-of-Things (IoT) framework, integrating a data fusion middleware customized from ITML’s Data Fusion Bus (DFB), and employing advanced ML algorithms for Business Intelligence purposes.
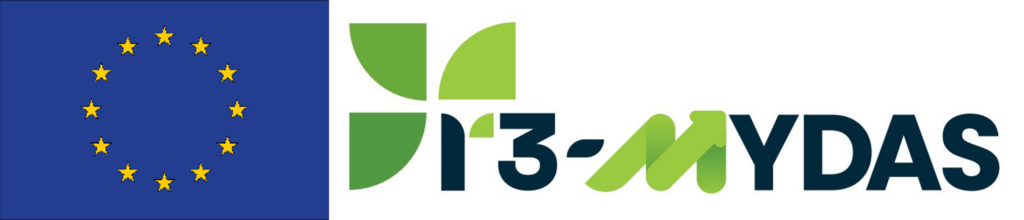
This project has received funding from the European Union’s Horizon Europe Research and Innovation program under grant agreement No101138738.
Find more information about the project: https://r3-mydas.eu/